How Much of Amazon Is Automated
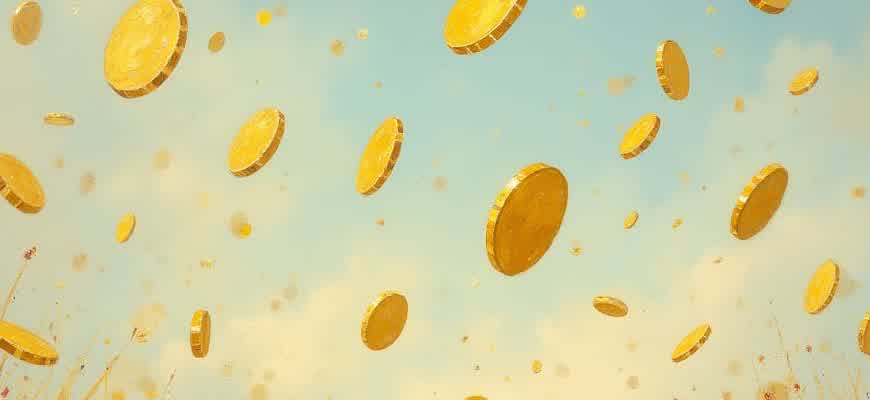
Amazon has integrated advanced automation systems across multiple layers of its business model, transforming its operational efficiency and logistics. From warehouses to delivery networks, automation plays a pivotal role in meeting the demands of global e-commerce.
Key Areas of Amazon's Automation:
- Warehouse Operations
- Order Fulfillment
- Supply Chain Management
- Customer Service and AI Support
Within Amazon’s vast infrastructure, robots, drones, and AI-driven systems handle tasks once performed by humans. The company's warehouse robots, for example, are responsible for picking and moving products quickly and accurately.
"Robotics and AI allow Amazon to process millions of items per day, drastically reducing human labor and increasing productivity." – Amazon Logistics Report
Automation in Numbers:
Area | Automation Level |
---|---|
Warehouse Operations | 75% Automated |
Order Fulfillment | 85% Automated |
Customer Support | 60% Automated |
Automation in Amazon Warehouses: A Deep Dive into Its Scope
The use of automation in Amazon’s fulfillment centers has transformed the logistics industry. Amazon deploys advanced robotics, machine learning, and automated systems to streamline its operations. This process allows the company to handle millions of orders efficiently by optimizing tasks such as sorting, inventory management, and product picking. Automated solutions are critical for Amazon’s ability to meet the rising demand for faster delivery times, especially during peak seasons like Black Friday or Prime Day.
However, automation within Amazon warehouses is not just about efficiency–it’s about scalability. The company relies heavily on AI algorithms to predict product demand and optimize the flow of goods throughout the warehouse. The combination of physical robots and intelligent software allows Amazon to handle ever-increasing volumes with fewer human resources required for manual tasks. While automation has made significant strides, human workers still play an essential role in overseeing operations and resolving complex issues.
Key Aspects of Automation in Amazon Warehouses
- Robot-Assisted Picking: Automated robotic arms fetch products from shelves, reducing human physical strain and speeding up order preparation.
- Inventory Optimization: AI systems predict and manage stock levels, ensuring products are readily available and minimizing storage inefficiencies.
- Sorting and Routing: Automated conveyor belts and sorting systems efficiently direct packages to the appropriate location, reducing human errors and delays.
- Packaging Automation: Machines automatically determine the best box size for each order, improving packing efficiency and reducing material waste.
Impact of Automation on Workforce and Efficiency
Automation in Amazon’s fulfillment centers enhances productivity but also necessitates a fine balance between human oversight and robotic assistance. This synergy ensures that operations are streamlined without losing the flexibility required to handle unique or complex tasks.
While automation in Amazon warehouses has led to a marked increase in efficiency, the reliance on automated systems also introduces new challenges. The human workforce continues to play a crucial role, especially in areas that demand adaptability and problem-solving that machines are not yet equipped to manage. Amazon’s investment in both robots and human workers ensures that the system remains robust and capable of scaling as demand grows.
Efficiency Gains from Automation
Automation Process | Efficiency Outcome |
---|---|
Robot-Assisted Picking | Speed of product retrieval increased by 40%, reducing order processing time. |
Inventory Management | Stock availability improved by 15%, reducing stock-outs and waste. |
Sorting and Routing | Order sorting accuracy increased by 30%, minimizing delays. |
Packaging | Reduced packaging time by 20%, leading to faster shipping processes. |
The Role of Robotics in Amazon's Warehousing System
In Amazon's fulfillment centers, robots play a critical role in streamlining operations. These automated systems are designed to enhance efficiency and reduce human labor requirements. Robots handle various tasks, from moving inventory to packing and sorting, ensuring that goods are processed quickly and accurately. By integrating robotics into its operations, Amazon has optimized its supply chain, significantly reducing the time it takes to fulfill customer orders.
With the rise of automation, Amazon's warehouses are becoming more advanced, utilizing a combination of robotic systems and AI to predict and respond to customer needs in real time. The integration of robotics has also allowed for a safer work environment, as robots handle the heavier, more dangerous tasks, freeing human employees for more specialized roles.
Types of Robots in Amazon Fulfillment Centers
- Kiva Robots: These robots are responsible for transporting shelves of products to human workers for picking and packing. Their mobility is central to reducing wait times between tasks.
- Robot Arms: These are used for sorting products, reducing errors and the time needed to sort individual items manually.
- Automated Guided Vehicles (AGVs): These vehicles transport goods across different sections of the warehouse, autonomously navigating the facility's layout.
Benefits of Automation
- Speed: Robots can work around the clock, speeding up the process of picking, packing, and shipping orders.
- Accuracy: Automated systems reduce the risk of human error, improving order accuracy and customer satisfaction.
- Cost Efficiency: Long-term, robots reduce labor costs and can perform tasks more quickly than human workers, leading to lower operational costs.
Automation in Amazon's Logistics Chain
Robot Type | Task | Impact on Operations |
---|---|---|
Kiva Robots | Transporting shelves of products to human workers | Improves speed and reduces walking time for workers |
Robot Arms | Sorting products | Increases sorting speed and reduces error rates |
AGVs | Transporting goods across the warehouse | Improves internal logistics and reduces manual handling |
"Robotics is an essential part of Amazon's vision for a faster, more efficient global supply chain."
How Amazon Leverages AI for Effective Inventory Management
Amazon has embraced AI-driven solutions to enhance the way it manages inventory, making it faster and more efficient. By using advanced algorithms, the company can predict demand, manage stock levels, and optimize warehouse operations. This AI-powered system is designed to minimize human error, reduce operational costs, and increase speed in restocking products.
One of the main components of Amazon's inventory management system is the ability to anticipate product needs based on historical data and real-time trends. AI-powered systems analyze consumer behavior, sales patterns, and even external factors like weather or holidays to predict what items will be in high demand.
Key AI Applications in Amazon's Inventory Process
- Demand Forecasting: Predicts product demand by analyzing large datasets, allowing Amazon to restock items proactively.
- Warehouse Automation: AI coordinates robots to manage storage, retrieval, and packaging tasks more efficiently.
- Dynamic Replenishment: Automatically adjusts stock levels based on real-time sales data and customer behavior.
How AI Improves Efficiency
Amazon's AI systems significantly reduce human intervention in managing stock levels, which leads to less overstocking or understocking. Additionally, AI-driven automation helps in managing the supply chain more efficiently by reducing delays and errors during order fulfillment.
"AI allows Amazon to manage billions of items across its network of fulfillment centers, optimizing every step of the inventory lifecycle from order placement to delivery."
Table: AI-Powered Inventory Management vs Traditional Methods
Aspect | AI-Powered Management | Traditional Methods |
---|---|---|
Demand Prediction | Uses historical and real-time data to predict future needs | Relies on manual data analysis and past trends |
Speed of Stocking | Automation handles restocking quickly and with precision | Slower, often relying on human labor for inventory checks |
Inventory Errors | Minimized through continuous data processing | More prone to human error and outdated data |
Automation in Amazon’s Shipping and Delivery Process
Amazon has revolutionized its shipping and delivery process by incorporating various levels of automation. From the moment an order is placed to the time it reaches the customer, Amazon’s fulfillment network leverages cutting-edge technology to improve efficiency and speed. This transformation has significantly reduced human intervention, particularly in sorting, packaging, and delivery stages.
As part of this automation, Amazon has developed advanced systems like robotics, machine learning, and autonomous vehicles. These innovations play a critical role in scaling operations while maintaining cost-effectiveness. Here's an overview of how automation integrates into Amazon's logistics.
Key Elements of Automation in Amazon's Shipping System
- Robotic Sorting: Robots handle the sorting process at fulfillment centers, quickly identifying products and categorizing them based on destination.
- Automated Packaging: Automated systems help package orders efficiently, ensuring they are ready for delivery without requiring manual labor.
- Last-Mile Delivery with Drones: Amazon is also testing drone delivery systems to automate the last-mile process, reducing the need for human drivers.
- Self-Driving Delivery Vehicles: Amazon is experimenting with autonomous vehicles for package delivery, aiming to reduce delivery times and costs.
Automation in Amazon’s shipping process significantly reduces human error, minimizes delays, and allows the company to scale operations without a corresponding increase in labor costs.
Technology Behind Amazon's Automated Logistics
- Robotics: The robots, such as the Kiva robots, move products across the warehouse floor, drastically reducing the time taken for stock retrieval.
- Machine Learning: Machine learning algorithms optimize routes for delivery and improve inventory management based on real-time data.
- AI-powered Forecasting: Predictive analytics help forecast demand and ensure products are stored in fulfillment centers closer to customers.
Impact of Automation on Delivery Times and Costs
Automation Component | Impact on Delivery | Cost Reduction |
---|---|---|
Robotic Sorting | Speeds up package sorting and shipping | Reduces labor costs |
Autonomous Vehicles | Decreases delivery times for long-distance orders | Minimizes driver-related expenses |
AI Forecasting | Improves inventory management, reducing stockouts and delays | Optimizes warehouse space, lowering storage costs |
Automation in Amazon's Customer Service: The Role of AI
Amazon has made significant strides in automating its customer service operations, leveraging artificial intelligence to handle a large portion of customer interactions. The use of AI helps Amazon address customer issues more efficiently, saving time for both customers and support staff. From automated chatbots to AI-driven voice assistants, Amazon is increasingly relying on technology to enhance its service delivery.
The integration of AI has allowed Amazon to scale its customer service capabilities, ensuring 24/7 availability without the need for constant human supervision. With AI systems processing large volumes of requests, Amazon has been able to focus human resources on more complex cases, while routine queries are handled by automated systems.
Types of AI Involved in Customer Service
- Chatbots – Handle basic inquiries, order tracking, and returns processing.
- Voice Assistants – Used through Amazon Alexa to resolve customer issues hands-free.
- Machine Learning Algorithms – Assist in predicting customer issues based on past interactions.
How Much AI Handles Customer Service?
AI currently handles the majority of simple customer queries, but human agents are still required for more complicated matters. The table below illustrates the typical division of labor between AI and human representatives in Amazon’s customer service ecosystem:
Task | AI Involvement | Human Involvement |
---|---|---|
Order Tracking | 85% | 15% |
Returns/Refunds | 80% | 20% |
Technical Support | 60% | 40% |
"Amazon’s AI-driven customer service systems are designed to handle a wide range of routine requests, freeing up human agents to focus on more nuanced issues."
The Effect of Automation on Amazon's Workforce Dynamics
Automation has significantly transformed the structure of Amazon's workforce, particularly in the warehouse and logistics sectors. Robots, AI, and machine learning technologies are increasingly taking over tasks that were once performed manually. This has led to a shift in the roles and responsibilities of Amazon employees. Many workers are now required to operate, supervise, and maintain automated systems, changing the traditional job descriptions within the company.
As more tasks are automated, the demand for certain types of roles, such as pickers, packers, and sorters, has decreased, while positions involving technology, programming, and robotics maintenance have increased. The transition has impacted not only job availability but also the skill sets required from employees. Amazon has responded by investing in upskilling initiatives to help workers transition into these evolving roles.
Impact on Job Roles
- Manual Labor Reduction: Many repetitive, physically demanding tasks are now handled by machines, reducing the need for human involvement in tasks such as sorting packages and transporting items.
- Shift to Tech-Heavy Roles: The increased reliance on robotics and AI means that employees now focus on tasks related to machine oversight, troubleshooting, and system optimization.
- Job Displacement and Creation: While some low-skill positions are disappearing, new opportunities arise in the form of high-tech roles, such as automation engineers and data analysts.
Key Changes in Employee Functions
- Machine Supervision: Workers now monitor and ensure the functionality of automated systems, requiring knowledge of machine learning algorithms and troubleshooting techniques.
- Maintenance and Repair: Employees must have skills in maintaining and repairing automated equipment, which is critical for preventing operational disruptions.
- Data Analysis: With the growing role of AI, employees are also expected to analyze data from automated systems to improve efficiency and productivity.
"Automation is not just about replacing labor, but about reshaping what it means to work in a warehouse environment."
Future Outlook
The introduction of automation is not expected to stop anytime soon. As Amazon continues to refine its processes, the workforce will need to adapt by acquiring more advanced technical skills. However, the full extent of automation's impact on Amazon employees' roles will depend on how quickly the company scales its use of AI and robotics, as well as its ability to retrain workers for these new tasks.
Role | Traditional Tasks | Automated Tasks | New Responsibilities |
---|---|---|---|
Warehouse Picker | Manual selection of items | Robot-assisted item retrieval | Supervision of automated picking systems |
Sorter | Manual sorting of packages | Automated sorting with AI | Maintaining and troubleshooting sorting systems |
Delivery Driver | Manual delivery of packages | Drone-assisted deliveries | Monitoring drone operations and maintenance |
Tracking Amazon’s Automation Investments and Future Plans in Cryptocurrency
Amazon has consistently made significant strides in automation, with a growing focus on incorporating blockchain technology and cryptocurrency into its operations. These advancements are not only changing the e-commerce landscape but also presenting new opportunities for integrating digital currency into Amazon’s ecosystem. As part of its long-term strategy, Amazon is investing in automation tools that can streamline transactions, enhance security, and offer more decentralized payment options for its customers globally.
Blockchain and automation are expected to merge more seamlessly in the coming years, and Amazon’s future plans suggest a more integrated approach to cryptocurrency. This would likely involve smart contracts, enhanced payment gateways, and automation in supply chain management using decentralized finance (DeFi) solutions. As Amazon continues to evolve, the automation of these technologies will play a key role in maintaining its competitive edge.
Amazon's Key Investments in Automation and Cryptocurrency
- Decentralized Finance (DeFi): Implementation of blockchain for secure, transparent, and fast transactions in Amazon's marketplace.
- Smart Contracts: Future automation of contracts through blockchain technology to improve efficiency and reduce manual processes.
- Automated Supply Chain Management: Use of blockchain and crypto solutions to monitor product movement and reduce fraud.
- Digital Currency Payments: Potential integration of cryptocurrency payment options for international customers.
Projected Timeline for Amazon’s Cryptocurrency Integration
- 2025: Initial integration of blockchain for logistics and transparency in transactions.
- 2026: Deployment of smart contract automation in global supply chain operations.
- 2027: Cryptocurrency-based payment systems implemented for select international markets.
Potential Impact on the Future
Amazon's focus on automation and cryptocurrency integration could revolutionize e-commerce by making transactions faster, more secure, and decentralized. This would not only benefit the platform but also give a significant boost to the wider adoption of digital currencies.
Investment Area | Projected Outcome |
---|---|
Blockchain Integration | Improved transaction transparency and speed |
Smart Contracts | Automated business agreements and reduced administrative costs |
Digital Currency Payments | Faster, secure, and cost-effective payment solutions |
Challenges and Limitations of Automation in Amazon Operations
Amazon's reliance on automation within its supply chain has revolutionized logistics and order fulfillment. However, despite the efficiencies gained, there are several challenges that limit the complete automation of their operations. These include the need for sophisticated algorithms, the high cost of maintaining cutting-edge technology, and the integration of new tools with legacy systems. Additionally, human oversight remains critical in ensuring the accuracy of complex processes, such as managing returns, handling exceptions, and overseeing product quality control.
Another significant challenge is adapting automation for the wide range of products that Amazon sells. Automation systems may be optimized for standard items but often struggle with irregular or fragile goods. This creates a need for hybrid models, where machines and humans work together. Furthermore, issues like system malfunctions or software bugs can severely disrupt operations, causing delays that counteract the benefits of automation.
Key Limitations of Automated Systems at Amazon
- Product Variety: Automated systems may struggle with handling diverse products, especially those with irregular shapes or fragile materials.
- Cost: The initial investment in robotics and advanced software, along with ongoing maintenance, remains a significant barrier.
- System Integration: Merging new technologies with older infrastructure presents ongoing technical and operational difficulties.
- Unforeseen Disruptions: Automation is susceptible to errors from software glitches, mechanical breakdowns, or unforeseen situations, which require human intervention.
Impact on Operational Efficiency
Although automation contributes significantly to Amazon’s operational efficiency, it is not a panacea. The hybrid approach–where human workers and automated systems complement each other–has proven to be essential in overcoming some of these limitations. However, Amazon must continue to innovate in addressing the gaps that automation alone cannot fill.
Automation brings efficiency, but human adaptability is still crucial for handling complex, non-routine tasks in dynamic environments like Amazon’s distribution centers.
Challenges in Automation Technology
Challenge | Impact |
---|---|
Adaptability to Product Types | Systems often fail to process unique or delicate products, causing delays and requiring human intervention. |
High Maintenance Costs | The cost of maintaining automated systems can erode profit margins if not carefully managed. |
Technological Failures | Software glitches or system breakdowns can significantly slow operations, demanding rapid problem-solving and recovery efforts. |