Industrial Robotic Automation Companies
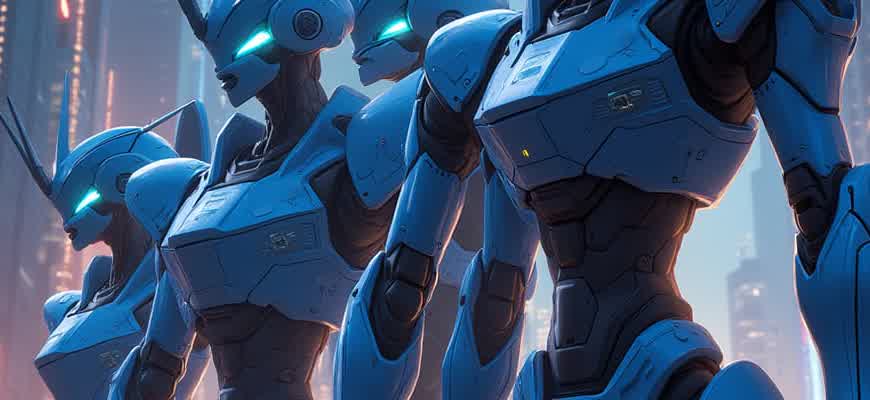
The integration of cryptocurrencies and blockchain technology into industrial robotic automation has transformed manufacturing and supply chain operations. Companies in this sector are increasingly adopting decentralized systems to optimize processes, reduce costs, and improve transparency.
Key Areas of Impact:
- Supply Chain Transparency: Blockchain ensures traceability and transparency of transactions between manufacturers, suppliers, and customers.
- Automation Efficiency: Cryptocurrencies provide a seamless way for companies to handle payments and financial transactions within automated systems.
- Security and Data Integrity: Decentralized ledger technology enhances the security of operational data, reducing the risk of cyber attacks.
Top Companies in Robotic Automation:
- ABB Robotics - A leader in industrial automation and robotics solutions for diverse industries.
- FANUC Corporation - Known for their highly efficient robotic systems and integration with IoT platforms.
- KUKA Robotics - Specializes in automation solutions for automotive, metal, and aerospace industries.
"The future of industrial automation is inherently tied to both robotics and blockchain, bringing greater efficiency and security to production environments."
Key Technologies and Trends:
Technology | Description |
---|---|
Blockchain | Enables secure, decentralized transactions in manufacturing and supply chain management. |
Robotic Process Automation (RPA) | Automation of repetitive tasks using robotics and AI to improve operational efficiency. |
IoT Integration | Links industrial robots with IoT devices for real-time data processing and decision-making. |
How to Select the Right Industrial Robotic Automation Partner for Your Business
Choosing the right industrial robotic automation partner can significantly impact your company's productivity, efficiency, and future growth. The right partner will help you navigate through complex integration processes and ensure that your automated systems are optimized for maximum performance. With the rise of advanced robotics, it is crucial to carefully evaluate potential partners based on their expertise, technological solutions, and ability to align with your specific business needs.
When selecting an automation partner, several key factors should be taken into consideration, including the partner’s experience in your industry, the scalability of their solutions, and their ability to provide ongoing support. Below are some important considerations to keep in mind:
Key Considerations for Selecting an Automation Partner
- Industry Expertise: Ensure the partner has experience in your specific industry. This will help minimize the learning curve and enable them to offer more tailored solutions.
- Customization and Scalability: The automation solutions should be flexible and scalable to adapt to your company’s changing needs.
- Technology Compatibility: The systems should be compatible with your existing infrastructure and should easily integrate with current technologies.
- Support and Maintenance: Look for partners that offer strong after-sales support and long-term maintenance services to ensure the smooth operation of automated systems.
Steps to Evaluate Potential Automation Partners
- Assess Their Portfolio: Review the projects the partner has completed and assess their success in industries similar to yours.
- Request Demos and Case Studies: Ask for demonstrations of their solutions in action and request case studies to evaluate their effectiveness in real-world scenarios.
- Evaluate Technical Support: Ensure the partner offers comprehensive support, including training, troubleshooting, and system upgrades.
- Consider Costs and ROI: Analyze the cost-effectiveness of the solution in relation to the long-term return on investment.
Remember that selecting an automation partner is a long-term decision. Make sure to choose a company that not only meets your immediate needs but can also grow with your business.
Comparison Table: Features to Evaluate
Feature | Partner A | Partner B |
---|---|---|
Industry Experience | 5 years in automotive | 10 years in electronics |
Technology Compatibility | High integration potential | Limited compatibility with legacy systems |
Support & Maintenance | 24/7 support | Business hours support only |
Customization | Highly customizable solutions | Standard solutions only |
Key Advantages of Robotic Automation in Manufacturing
The integration of robotic automation in the manufacturing industry offers a variety of compelling advantages that can drive growth, improve efficiency, and enhance overall performance. Robotics enables manufacturers to reduce costs, optimize production schedules, and maintain a consistent level of quality, regardless of demand fluctuations. By automating repetitive and complex tasks, manufacturers can increase throughput while decreasing the potential for human error, ultimately enhancing the bottom line.
Robots provide manufacturers with the flexibility to address specific needs in different production stages, improving agility in adapting to market changes. With faster cycle times and the ability to perform tasks at a level of precision that surpasses human capacity, companies gain a competitive edge. Additionally, the implementation of robotics helps optimize resource management by reducing waste and energy consumption, contributing to long-term sustainability goals.
Core Benefits of Implementing Robotics in Production
- Cost Efficiency: Robotic automation significantly reduces labor costs and lowers the risk of expensive human errors.
- Enhanced Productivity: Robots can operate continuously without breaks, increasing overall output and meeting tight deadlines.
- Improved Product Quality: Precision and consistency in production lead to fewer defects and higher-quality products.
- Safety and Ergonomics: Robotics can take over hazardous tasks, reducing workplace injuries and improving the safety of employees.
"Automation brings long-term financial savings, providing both increased efficiency and higher levels of safety in a competitive manufacturing environment."
Impact on Resource Utilization
Aspect | Effect of Robotic Automation |
---|---|
Labor | Reduction in manual labor, reallocating human resources to more strategic tasks. |
Material Waste | Minimization of material wastage through precise handling and task execution. |
Energy Consumption | Optimized energy usage due to increased efficiency of robotic systems. |
Overcoming Common Barriers in Adopting Robotic Automation in Industrial Sectors
Integrating robotic solutions into industrial processes can significantly improve efficiency, but the journey is rarely without obstacles. Companies often face numerous hurdles when trying to incorporate automation into their operations. The complexity of new technologies, high upfront costs, and workforce adaptation are just a few of the challenges that need to be addressed strategically to ensure successful deployment and maximum ROI.
One of the core challenges for companies looking to adopt robotic automation is the integration with existing infrastructure. Robotics solutions require considerable technical and logistical adaptations to make them compatible with current systems, which can be both time-consuming and costly. Below are some of the common issues faced during the implementation of industrial automation systems and the steps to mitigate them.
Key Challenges and Solutions
- High Initial Investment: The cost of robotic systems, installation, and maintenance can be prohibitive for smaller manufacturers.
- Complex Integration: Older infrastructure may require significant upgrades to work seamlessly with new robotic systems.
- Workforce Adaptation: Employees may resist the transition to automated systems, fearing job loss or a steep learning curve.
Tip: To overcome the high cost, companies should explore financing options, grants, or collaborations with tech providers to spread out the expense over time.
Approaches to Overcome These Challenges
- Careful Planning and Scalability: Implementing robotics incrementally, starting with less complex tasks, allows for testing and adjustment.
- Training and Workforce Engagement: Proactive training programs help employees embrace automation, making them feel more secure in their roles.
- Collaborative Solutions: Engaging with robotic vendors who offer customized integration support can ease the process and reduce complexity.
Challenge | Solution |
---|---|
Initial Investment | Seek financing options or government incentives to spread the cost over time. |
Integration Complexity | Gradual implementation and collaboration with experienced tech providers. |
Workforce Resistance | Offer training programs and involve employees in the process from the start. |
Exploring the Different Types of Industrial Robots Used in Automation
Industrial robotics is a key element of modern manufacturing, providing increased efficiency, precision, and flexibility in automated processes. The use of robots in industries like automotive, electronics, and food processing has drastically improved productivity while reducing labor costs. These robots are designed to perform repetitive tasks with high accuracy, ensuring consistent product quality and minimizing human error. As the technology evolves, the range of robots used in automation continues to expand, with each type offering distinct advantages for different applications.
Automation companies integrate various kinds of industrial robots depending on the specific needs of the manufacturing process. The main categories of industrial robots include articulated robots, SCARA robots, delta robots, and collaborative robots (cobots). Understanding the differences between these robot types helps companies choose the most suitable option for their automation systems, improving overall workflow and performance.
Types of Industrial Robots
- Articulated Robots: These robots are characterized by their rotating joints that provide a wide range of movement. They are ideal for complex tasks such as welding, painting, and assembly.
- SCARA Robots: Known for their speed and precision, SCARA robots are commonly used in high-speed assembly and pick-and-place operations. Their rigid arms offer excellent repeatability.
- Delta Robots: These robots are lightweight and capable of performing very fast, precise movements. They are often used for high-speed picking and packaging tasks in food and electronics industries.
- Collaborative Robots (Cobots): Cobots work alongside human operators, making them ideal for tasks that require flexibility and close interaction with workers. They are equipped with safety features to prevent accidents.
Each robot type has unique strengths that make it suitable for specific applications. For example, SCARA robots excel in speed, while delta robots are designed for high-precision operations. Collaborative robots, on the other hand, bridge the gap between human capabilities and robotic automation.
Note: When selecting an industrial robot, companies must consider factors like speed, payload capacity, precision, and flexibility in order to optimize their production lines.
Comparison Table
Robot Type | Application | Key Feature |
---|---|---|
Articulated Robots | Welding, Assembly | Flexible movement with multiple joints |
SCARA Robots | Assembly, Pick-and-Place | High-speed precision |
Delta Robots | Packaging, Picking | Fast and precise movements |
Collaborative Robots | Assisting humans, Flexible operations | Safe interaction with humans |
Cost Factors to Consider When Investing in Robotic Automation
When considering an investment in robotic automation, it's essential to understand the different cost elements involved. While robotics can greatly improve efficiency and reduce long-term labor expenses, the initial investment can be substantial. Various factors such as hardware, software, and maintenance must be taken into account to accurately forecast total expenses. Cryptocurrency investments can be compared in terms of volatility and long-term value, with similar unpredictability in technological advancements, as both markets demand careful planning and risk management.
These expenses aren't always straightforward, and it’s important to break them down. Here's what to expect when planning a robotic automation implementation, especially for companies that aim to leverage advanced technologies like blockchain in their automation systems.
Key Considerations in Costing Robotic Automation Systems
- Initial Capital Investment: The upfront costs for robotic systems, including hardware (robots, sensors, etc.), installation, and integration with existing workflows.
- Software Development & Licensing: Depending on the complexity of your automation system, bespoke software development or licensing costs may vary significantly.
- Maintenance and Support: Ongoing operational expenses such as software updates, parts replacement, and technician services.
- Training and Skill Development: Ensuring that your team can effectively work with robotic systems often requires specialized training.
"The true value of robotic automation goes beyond just the initial cost; it lies in the operational efficiencies and long-term savings achieved through optimized processes and reduced human error."
Investment Comparison: Cryptocurrency vs. Robotic Automation
Factor | Cryptocurrency Investment | Robotic Automation Investment |
---|---|---|
Initial Investment | High volatility, unpredictable entry costs | Fixed costs for hardware, software, installation |
Long-term Value | Highly speculative with possible high returns | Stable returns through productivity and efficiency gains |
Risk | Market-driven fluctuations | Operational risks tied to system integration and maintenance |
Conclusion
Both robotic automation and cryptocurrency investments come with inherent risks and rewards. While automation promises measurable productivity gains, it requires a high initial investment and ongoing operational costs. Understanding these factors can help you make a more informed decision about how to balance both short-term expenses and long-term returns.
Integrating Robotic Automation into Established Manufacturing Systems
Adapting industrial robots into an existing production line can be a complex yet highly rewarding process. For companies already operating on traditional machinery, incorporating automation requires thoughtful planning, strategic integration, and thorough evaluation of current workflows. The goal is not only to enhance productivity but also to ensure that robotic systems complement existing operations, rather than disrupt them. Before diving into the integration process, it’s essential to identify the areas where automation will deliver the most value and streamline production cycles.
The integration process can be broken down into several stages: assessing current workflows, selecting the right robotic system, and implementing the technology with minimal downtime. By addressing each phase carefully, manufacturers can maximize the benefits of industrial robots, including higher efficiency, lower error rates, and increased overall capacity. Additionally, ensuring that robots work seamlessly with existing machinery and human workers is key to success.
Key Steps to Effective Integration
- Conduct Workflow Analysis: Review existing operations to identify bottlenecks and areas where automation would add value.
- Select the Right Robotic Solution: Choose a robot that suits the specific tasks to be automated, considering factors like payload, reach, and precision.
- Invest in Employee Training: Provide training to workers on how to collaborate with robotic systems and ensure smooth human-robot interaction.
- Ensure Compatibility: Make sure the robotic system integrates well with legacy machinery and factory infrastructure.
- Plan for Maintenance: Establish a maintenance schedule to keep robots running at peak efficiency.
Considerations for a Smooth Transition
Integrating robots into existing processes can significantly reduce production costs and improve quality. However, the transition should be managed carefully to avoid disrupting day-to-day operations.
When introducing robotic automation, manufacturers should consider the following factors:
- Automation Flexibility: Ensure the system can be adjusted or expanded as production needs change.
- Data Connectivity: Implement sensors and software that allow robots to communicate effectively with other systems on the production floor.
- Cost of Integration: Calculate the long-term ROI of automating specific tasks to justify the initial investment in robotics technology.
Example of Robotic Integration Process
Step | Action |
---|---|
1 | Analyze existing production processes to determine areas for automation. |
2 | Select and customize the appropriate robotic systems for the tasks. |
3 | Install and integrate robots with minimal disruption to the current production line. |
4 | Train operators and maintenance personnel to work with the new automated systems. |
5 | Monitor system performance and adjust as necessary for optimization. |
Real-World Case Studies: Success Stories from Robotic Automation Companies
Several companies in the industrial robotic automation sector have experienced remarkable success by integrating advanced robotics and AI into their operations. These technologies have drastically improved productivity, reduced operational costs, and enhanced overall efficiency. Here, we explore some of the key real-world applications that highlight the significant advantages of robotic automation in various industries.
One prime example is the implementation of robotic automation in the automotive manufacturing industry. By automating critical processes, manufacturers have significantly reduced the need for human labor in dangerous environments while increasing precision and consistency. These efforts have led to faster production rates and improved safety standards across the board.
Case Study 1: Automotive Industry
In the automotive sector, a leading manufacturer deployed robotic arms to automate assembly lines. This transition helped streamline production processes, reducing cycle times by over 40%. Below are some key results:
- Reduction in labor costs: Automation replaced manual labor for repetitive tasks, cutting down labor costs by 30%.
- Improved quality control: Robots consistently meet high precision standards, reducing defects by 20%.
- Enhanced safety: Dangerous tasks are now handled by robots, leading to a 50% reduction in workplace injuries.
"The integration of robotic systems into our production line has transformed our operations. We've seen both cost savings and improvements in product quality," said the operations manager of the automotive company.
Case Study 2: Electronics Manufacturing
In the electronics industry, robotic automation has been pivotal in the assembly of sensitive components. A notable example is a global electronics company that adopted robots for component placement and soldering. This transition not only improved production speed but also ensured a higher standard of quality.
- Faster throughput: Production speed increased by 25%, allowing faster product delivery times.
- Enhanced precision: Automated systems consistently place micro-components with micron-level accuracy, reducing errors.
- Cost efficiency: With automation, the company reduced production costs by 18% over a 12-month period.
Metric | Before Automation | After Automation |
---|---|---|
Production Speed | 100 units/hour | 125 units/hour |
Cost per Unit | $5.00 | $4.10 |
"Adopting automation has revolutionized our approach to assembly. Not only did we reduce defects, but we also achieved significant cost reductions," said the CEO of the electronics manufacturer.